Last note on the heated grips failure.
I finally got a chance to check the ST charging system a few weeks ago. Between two snow storms…
The charging system began with a nice 14.3V at the battery. Good. Checked the ripple with my scope. All phases checked present. Very good! So where’s the problem?
A design flaw?
Since the alternator is installed inside the “V” and provides a built in negative voltage temperature compensation, as the engine warms up to operating temperature, standing still in the driveway, the voltage starts to lower, following the increase of the engine temp.
Here it is, the output voltage of the alternator is quite influenced by the engine temperature. This changes everything, especially if you are moving at a low pace or in a stop & go traffic. The voltage could drop into the middle to low 13V. Independent of the ambient temperature surrounding the motorcycle. That, combined with the drop in voltage through the wiring, brought my heated grip outside the operation range.
This is the situation when I noticed the problem that started the whole process. Basically, the ambient temperature was too warm and I was caught in a very slow traffic. I just checked my heated grips… for fun.
So, I am keeping the mod, which eliminates most of the voltage drops. Moreover, I went full on, and I checked for the killing green crusty on every power connector. And yes, there were some. Not extreme, but all have been deoxidized and lubricated.
I also doubled the “crazy” undersized ground run at the big white (natural) connector.
Ready, right on for the start of the too short motorcycle season… in Canada/Québec.
Everybody, thanks for your support!
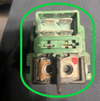
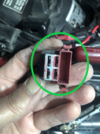
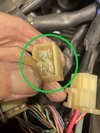
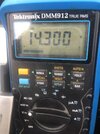
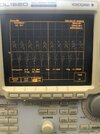