Today was rear-brake-caliper and general cleaning day.
Started with this:
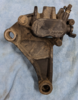
Normally I wouldn't remove the pistons from the calipers, but given the yucky that came out of the brake-lines I decided I should. I purchased all-balls rebuild kits and then removed the pistons using compressed air (not a job for the faint hearted IMHO):
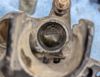
Glad I did as it was full of crud. The pistons were a little rough:
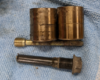
I proceeded to cleanup the mounting frame:
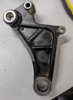
While the ultrasonic cleaned up the rest:
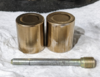
I gave the swingarm an elbow-grease-once-over and removed the rear brake line (in preparation to replace it with the steel line):
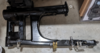
Then I moved on to the switch gear. The hi/low was a little wonky when the bike was parked so I sprayed contact cleaner in the contacts:
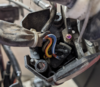
Accidentally dropped a screw:
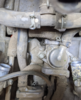
So many places for screws to hide!
Found it:
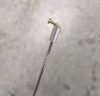
Contacts aren't overly clean:
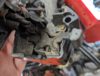
Spent a while making it better.
Anyone ever paint the fiberglass around the kill switch? Looks a little road-worn:
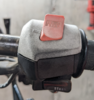
But the bike is looking good:
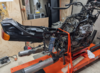
Super excited to start more re-assembly soon. Looks like a bike exploded across my garage....
Barry
Started with this:
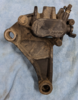
Normally I wouldn't remove the pistons from the calipers, but given the yucky that came out of the brake-lines I decided I should. I purchased all-balls rebuild kits and then removed the pistons using compressed air (not a job for the faint hearted IMHO):
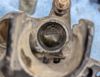
Glad I did as it was full of crud. The pistons were a little rough:
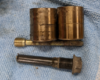
I proceeded to cleanup the mounting frame:
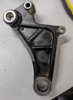
While the ultrasonic cleaned up the rest:
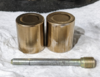
I gave the swingarm an elbow-grease-once-over and removed the rear brake line (in preparation to replace it with the steel line):
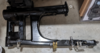
Then I moved on to the switch gear. The hi/low was a little wonky when the bike was parked so I sprayed contact cleaner in the contacts:
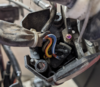
Accidentally dropped a screw:
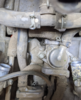
So many places for screws to hide!
Found it:
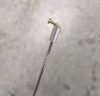
Contacts aren't overly clean:
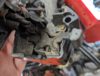
Spent a while making it better.
Anyone ever paint the fiberglass around the kill switch? Looks a little road-worn:
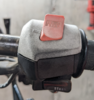
But the bike is looking good:
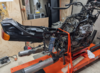
Super excited to start more re-assembly soon. Looks like a bike exploded across my garage....
Barry