When doing an oil change on my 2003 ST1300, I removed a screw for a cover on the top of the engine (above the oil filling cap) and put it back but it keeps popping back out, not sure how to put it back in, it feels like is in ( the thread doesn’t look or feel stripped) but when I start the engine it has a knocking sound and the screw rattles. Do I have to take the whole thing apart to put the screw back ?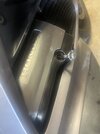
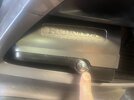
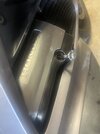
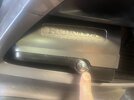